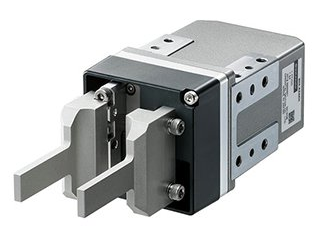
A gripper is a crucial component in automation systems, often used as an end-effector at the end of a robotic arm or on a Cartesian robot. It's designed to grasp and transfer objects from one point to another. However, it's more than just closing jaws—it requires precise control to avoid damaging delicate items.
In this post, we’ll explore how to properly use a gripper to handle sensitive loads without causing damage.
CHALLENGE |
Grip a delicate part without damaging it
|
Â
![Gripping a delicate load]()
Imagine handling a test tube filled with virus samples—this is a perfect example of a delicate load. The gripper must not only be accurate but also adjust grip force and speed automatically to prevent excessive pressure or impact. This concept applies to various types of sensitive materials beyond just test tubes.
SOLUTION |
EH Series gripper system with stored push motion and speed data settings
|
The EH Series gripper uses a dual rack and pinion system with two base jaws. As the motor rotates the pinion, both jaws move simultaneously with a positioning accuracy of +/-0.02 mm. This system allows for flexibility in gripping different types of loads by swapping out pincers or arms. The design ensures consistent performance and precision.
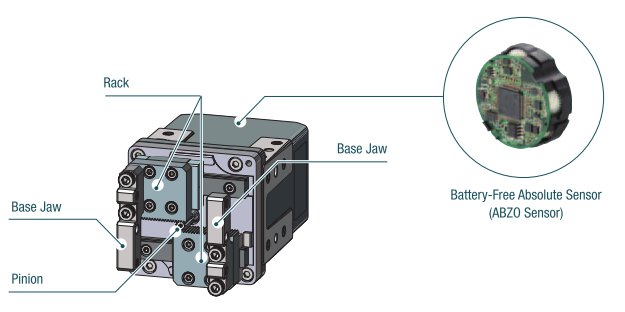
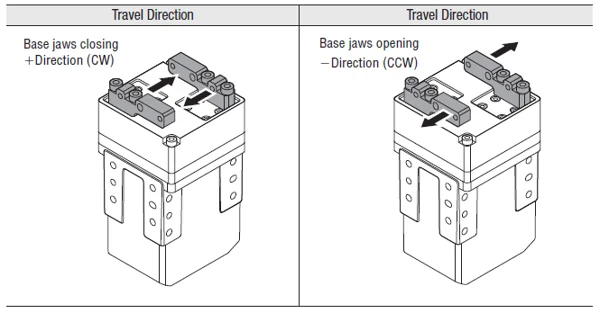
Multiple driver options are available, including Pulse Input, RS-485, EtherCAT, and EtherNet/IP. These allow for flexible integration into different automation setups. For instance, the Pulse Input driver is ideal for users who prefer traditional step/direction commands, while the RS-485 driver enables remote monitoring and control through networks.
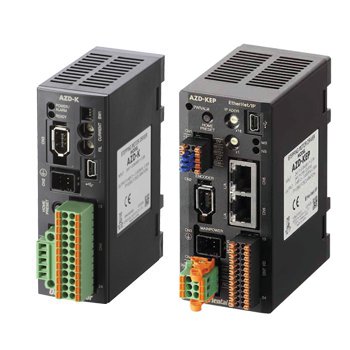
The EH Series includes a battery-free absolute sensor (ABZO sensor), eliminating the need for external sensors or batteries. This feature simplifies installation and reduces maintenance. Additionally, AlphaStep hybrid control technology ensures reliable operation and prevents missed steps, making it ideal for high-precision applications.
For this guide, we'll focus on the Stored Data (RS-485) driver, which can store up to 256 motion profiles. These profiles include position, push motion settings, and speed data. Once programmed using the MEXE02 software, they are stored within the driver and can be triggered via BCD inputs, either physically or over a network.
What Is Push Motion?
Push motion is a technique that limits the torque of a stepper motor by controlling its current. By adjusting the current in 1% increments, the grip force can be precisely controlled. This is especially important when handling fragile items like test tubes or medical samples.
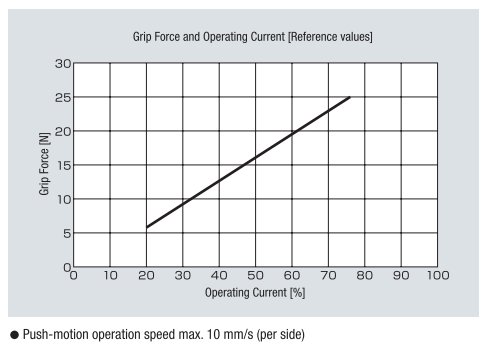
|
Now that we understand the key components of the EH Series gripper system, let’s look at how to properly use it to handle delicate loads without causing damage.
Key Point |
Use push motion with multiple speed settings to minimize impact force and impact
|
By linking multiple motion profiles together, you can create a continuous sequence with varying push motion force and speed settings. This allows the gripper to approach the object quickly, slow down as it gets close, and then gently grip the item. Once the desired grip force is achieved, the gripper holds it constant until the part is released.
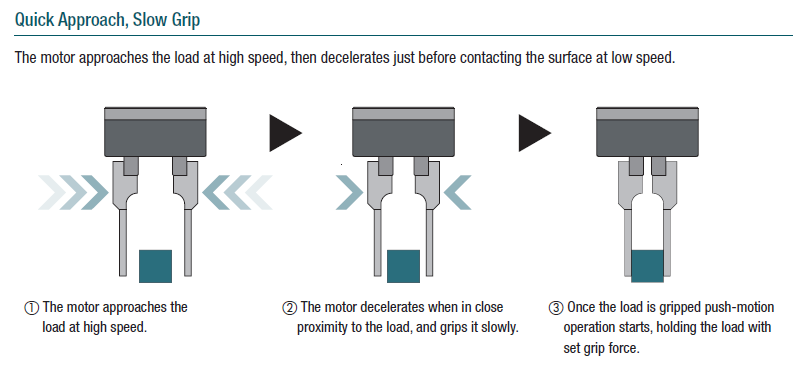
Let’s take a closer look at how this works with a soft load, like a sponge. A video demonstration shows the smooth and controlled movement of the gripper during the process.
Next, let’s see how variable speed operations can enhance the process. Another video demonstrates how the gripper adjusts its speed to ensure a smooth and safe grip.
The EH Series also features built-in mechanical absolute encoders that can detect the load or confirm its dimensions. The driver provides outputs such as TLC (Torque Limiting Control), MOVE, and AREA, which can be accessed physically or remotely over a network.
- TLC Output: Activates when the set grip force is reached.
- MOVE Output: Activates when the motor is moving.
- AREA Output: Activates when the motor is within a specific position range.
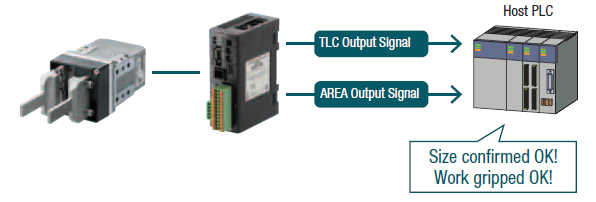
Another video shows how these outputs work in practice, confirming the grip force and the size of the load.
If wiring isn’t your preference, the same operation can be performed via network command with a status monitoring function.
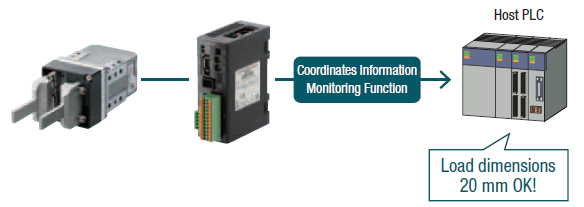
Conclusion
By combining push motion, speed settings, mechanical absolute encoder output, and driver outputs like TLC, MOVE, and AREA, the EH Series gripper system offers a reliable and efficient way to handle delicate parts. This makes it ideal for applications where precision and care are essential.
hbspt.cta._relativeUrls=true;hbspt.cta.load(2284573, 'fdb88bb6-1bf6-4f5d-a90e-f5d82f1c1eb5', {"useNewLoader":"true","region":"na1"});
hbspt.cta._relativeUrls=true;hbspt.cta.load(2284573, 'fad37be8-6d75-4fd1-93df-2ea7037b188a', {"useNewLoader":"true","region":"na1"});
Simplify your setup and control by using products from the same AlphaStep family. All AlphaStep products with AZ Series mechanical encoder technology use the same dedicated drivers, making it easy to add new axes. Motion data and parameters can also be transferred between axes. To help shorten the learning curve, software training videos are available.
hbspt.cta._relativeUrls=true;hbspt.cta.load(2284573, '59c67a88-c8f7-452d-8792-36ff47c50ace', {"useNewLoader":"true","region":"na1"});
hbspt.cta._relativeUrls=true;hbspt.cta.load(2284573, '39ae2306-a4c3-4ac6-ad3c-749ca7c0cb64', {"useNewLoader":"true","region":"na1"});
hbspt.cta._relativeUrls=true;hbspt.cta.load(2284573, 'c9cd6ed1-0aa4-4485-aba4-c8a4b3128d90', {"useNewLoader":"true","region":"na1"});
Thanks for reading! Don’t forget to subscribe if you want to stay updated on our latest posts and product updates.
Aluminum Alloy Pressure Cooker
JIANGMEN WOHAO IMPORT AND EXPORT CO.,LTD , https://www.funghogroup.com