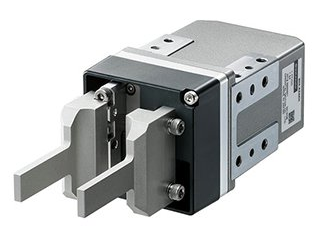
A gripper is a crucial component in automation systems, typically mounted at the end of a robotic arm or cartesian robot. Its main function is to grasp and move parts from one location to another. However, the process involves more than just closing the jaws—it requires careful control to prevent damage to delicate items.
In this article, we'll explore how to properly use a gripper to handle sensitive loads without causing any harm.
CHALLENGE |
Grip a delicate part without damaging it
|
Â
![Gripping a delicate load]()
Imagine handling a test tube filled with virus samples—this is a perfect example of a delicate load that needs precise gripping. The gripper must adjust its force and speed automatically to avoid applying too much pressure or causing impact. This principle applies not only to test tubes but also to various other types of sensitive materials.
SOLUTION |
EH Series gripper system with stored push motion and speed data settings
|
The EH Series gripper uses a dual rack and pinion design with two base jaws. As the motor rotates the pinion, both jaws can extend or retract simultaneously with high precision—up to +/-0.02 mm. It supports different gripper arms for various load types, making it versatile for many applications.
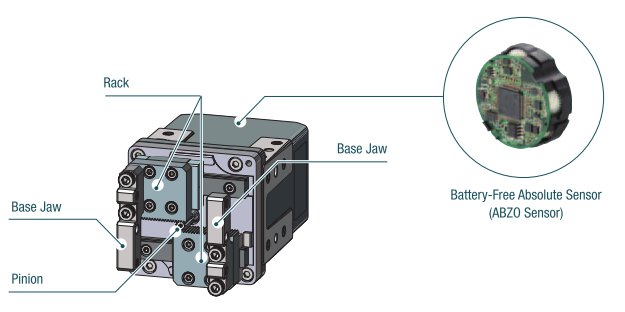
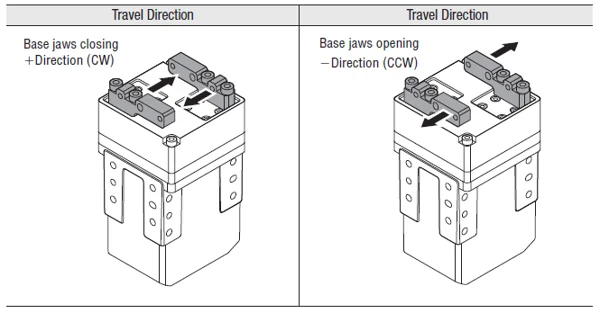
There are several driver options available, including Pulse Input, RS-485, EtherCAT, and EtherNet/IP, allowing for flexible integration into different systems.
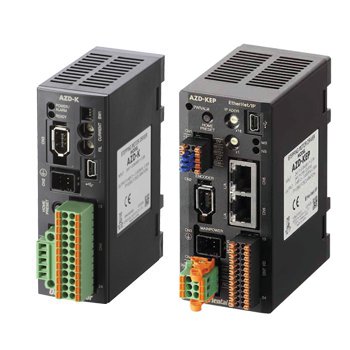
- Pulse Input
- Pulse Input + Stored Data (RS-485)
- Stored Data (RS-485)
- EtherCAT (1-4 axes)
- EtherNet/IP (single axis)
- Other industrial communication protocols available with network converters
|
The EH Series includes features like battery-free absolute sensors and AlphaStep hybrid control technology, which ensure reliable operation and reduce maintenance needs.
For this example, we’ll focus on the Stored Data (RS-485) driver, which can store up to 256 motion profiles. These include position, speed, and push motion settings. Once programmed using MEXE02 software, these profiles can be executed via BCD inputs, either physically or over a network.
What Is Push Motion?
Push motion limits the torque of a stepper motor by controlling its current. Since torque is proportional to current, adjusting it in 1% increments allows for precise grip force control.
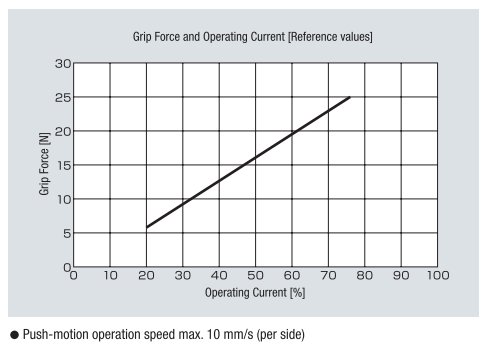
|
Now that we understand the components, let’s look at how to use the EH Series to safely grip a load.
Key Point |
Use push motion with multiple speed settings to minimize impact force and impact
|
With the linked motion sequence function, you can create a continuous motion profile with varying push forces and speeds. For example, a gripper can approach a test tube quickly, slow down when close, and grip it gently once in position.
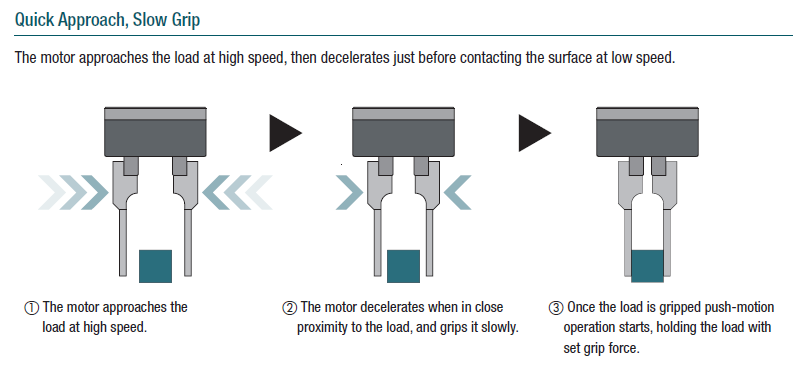
To see this in action, check out the video below.
Additionally, the built-in mechanical absolute encoder helps detect the load or confirm its size. The driver provides outputs such as TLC, MOVE, and AREA, which can be used to monitor grip force and position effectively.
- TLC Output: activates when a set grip force is reached
- MOVE Output: activates when the motor is moving
- AREA Output: activates when the motor is within a specific position range
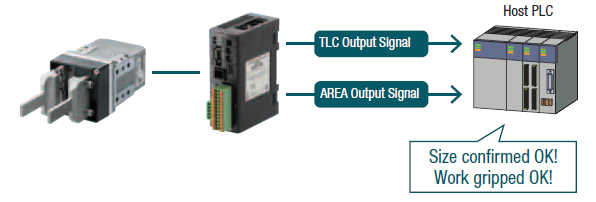
Finally, the EH Series offers a reliable and efficient way to handle delicate loads, ensuring minimal risk of damage while maximizing performance.
Conclusion
By combining push motion, speed control, and advanced sensor feedback, the EH Series gripper system ensures safe and accurate handling of even the most sensitive materials.
hbspt.cta._relativeUrls=true;hbspt.cta.load(2284573, 'fdb88bb6-1bf6-4f5d-a90e-f5d82f1c1eb5', {"useNewLoader":"true","region":"na1"});
hbspt.cta._relativeUrls=true;hbspt.cta.load(2284573, 'fad37be8-6d75-4fd1-93df-2ea7037b188a', {"useNewLoader":"true","region":"na1"});
Simplify your setup and control by using products from the same AlphaStep family. All AlphaStep products with AZ Series encoders use the same drivers, making installation and configuration quick and easy. You can transfer stored motion data between axes, further streamlining your workflow.
hbspt.cta._relativeUrls=true;hbspt.cta.load(2284573, '59c67a88-c8f7-452d-8792-36ff47c50ace', {"useNewLoader":"true","region":"na1"}); are available.
hbspt.cta._relativeUrls=true;hbspt.cta.load(2284573, '39ae2306-a4c3-4ac6-ad3c-749ca7c0cb64', {"useNewLoader":"true","region":"na1"});
hbspt.cta._relativeUrls=true;hbspt.cta.load(2284573, 'c9cd6ed1-0aa4-4485-aba4-c8a4b3128d90', {"useNewLoader":"true","region":"na1"});
Thanks for reading! Don’t forget to subscribe for more updates on robotics and automation solutions.
Coffee Maker
Coffee Stir Sticks,Wooden Coffee Stir Sticks,Coffee Roasting Supplies,Restaurant Depot Coffee Maker
JIANGMEN WOHAO IMPORT AND EXPORT CO.,LTD , https://www.funghogroup.com